Cork insulation boards
Origin | Portugal |
Usage | Wall (interior), floor / ceiling (interior) |
Average bulk density | 120 kg/m³ |
Thermal conductivity | 0,04 W/(mK) |
Fire protection class | E |
Specific heat capacity | 2.100 J/(kgK) |
CO₂ balance (global warming potential – GWP): | 15,99 kg CO2-Equivalent/m³ |
Recycable, closed loop |
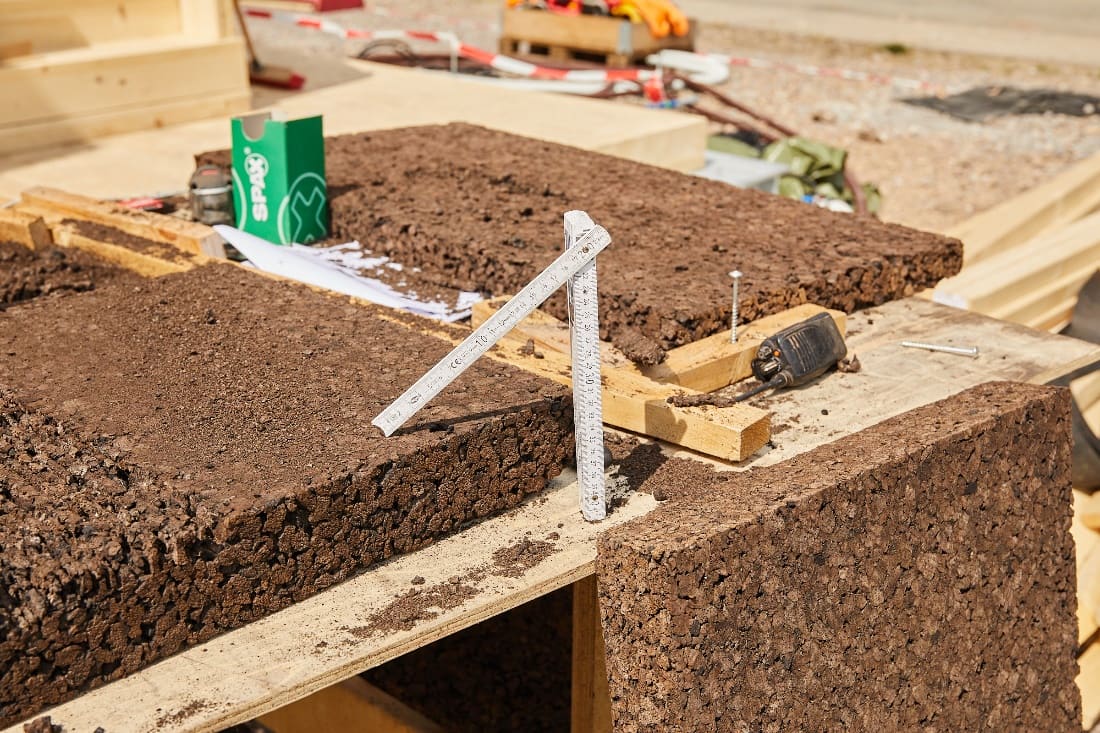
Cork is a monomaterial and contains neither component layers nor additives. The natural resistance of the material ensures that no additional protection against fire, mold and pests is required. It is a renewable raw material which has its origin in Portugal. After the cork oak reaches the age of 25, its bark can be removed every nine years. When the bark is harvested, no harm is done to the tree, which allows it to produce cork again and again. After the cork bark is harvested, it is ground. The cork meal is expanded by superheated steam (approx. 350°), thereby unfolding its cork’s own resin content (suberin). This resin acts as a binder and ensures that no additional substances are required to strengthen the cork insulation board.
The purity of the material makes it 100% compostable and recycable. Cork has positive properties, such as low weight. It can insulate both heat and sound. In addition, cork is very insensitive to moisture and has virtually no wear. It is a durable and resistant material.
The cork insulation boards are screwed to the solid wood wall with stainless steel screws. This provides a quickly removable connection technique.
The cork boards are visibly repurposed as wall cladding in the HDU, but are largely hidden as insulation material behind the façade and in the floor and ceiling of the residential modules.
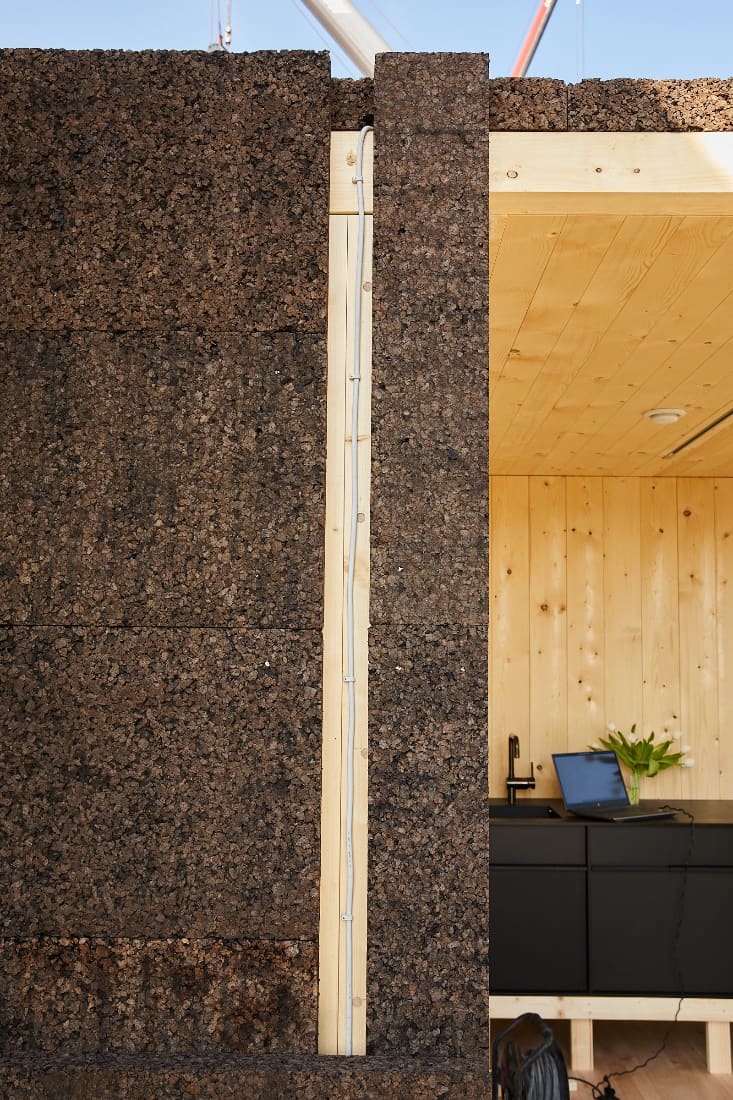
Solid Wood Element
Origin | South Tyrol, Italy |
Usage | Wall (structural), floor / ceilings (interior) |
Average bulk density | 420 kg/m³ |
Thermal conductivity | 0,11 W/(mK) |
Fire protection class | D |
Specific heat capacity | 1600 J/(kgK) |
CO₂ balance (global warming potential – GWP): | -3,64 kg CO2-Equivalent/m³ |
Recycable, closed loop |
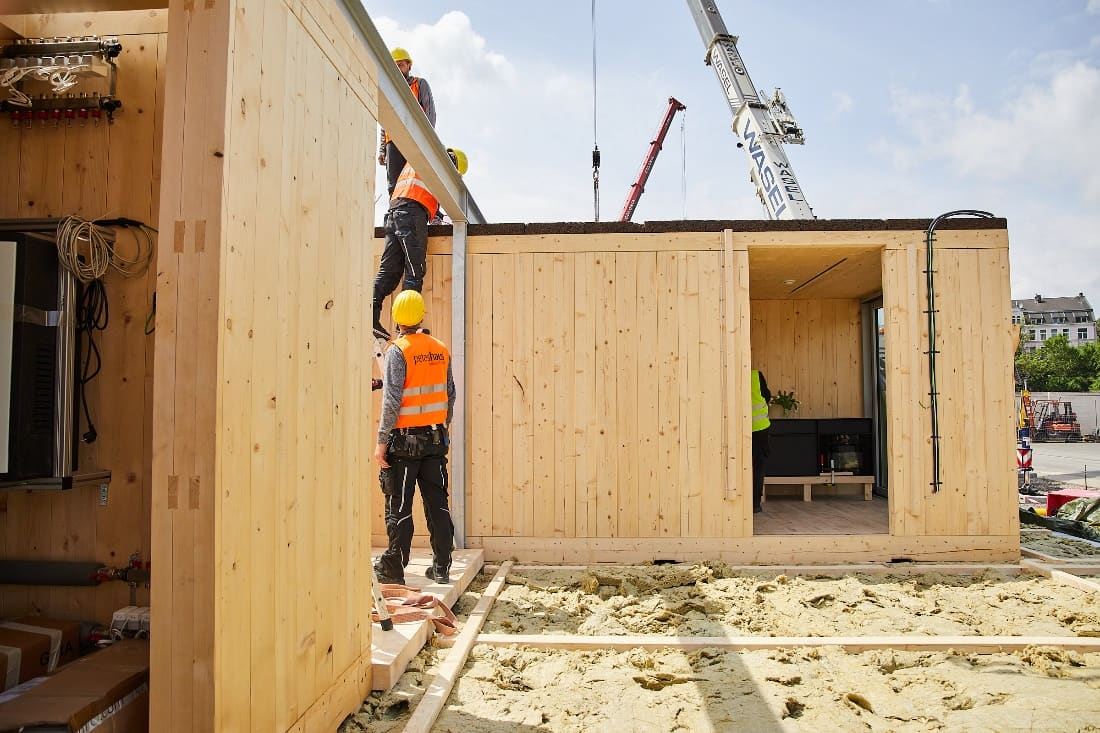
From sustainable sawn timber (PEFC certificate), the wooden elements are first dried in a drying chamber to a moisture content of approx. 13%. Then, dovetail joints are milled into the planks with the help of modern production equipment and thus tailor-made pre-produced. The solid wood elements are joined together in an airtight manner using tongue and groove joints. Therefore, no foil is needed here for sealing. The element is thus manufactured completely without glue or metal and can be easily dismantled due to the plug-in connection. The wood can be composted for disposal or thermally recycled.
Replacing a typical wall cladding in the living room with wood, especially enriches the well-being of users due to the natural color, vivid surface and even improves the indoor climate. The cells in the wood naturally regulate the humidity of the air. The elements are not only fire tested, but in some cases have better fire behavior than conventional building materials. The CO2-neutral building material can be used flexibly and in many ways because of its many positive properties.
All three modules of the HDU are built as wall/floor and ceiling elements with these load-bearing solid wood elements. Behind the kitchen in the living module, the individual elements can be seen particularly well.
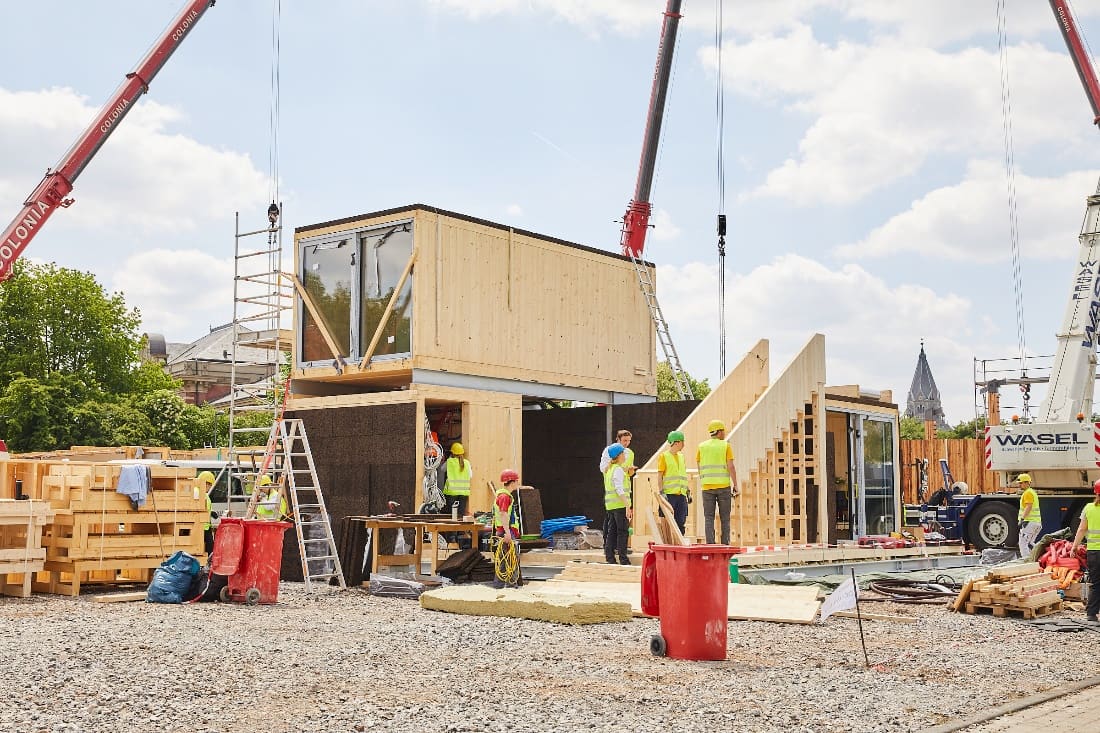
Wood Fiber Insulation
Origin | Waldshut-Tienge, Germany |
Usage | Wall (interior), floor/ceiling (interior) |
Average bulk density | 167 kg/m³ |
Thermal conductivity | 0,037 – 0,047 W/(mK) |
Fire protection class | E |
Specific heat capacity | 2.100 J/(kgK) |
CO₂ balance (global warming potential – GWP): | -91,14 kg |
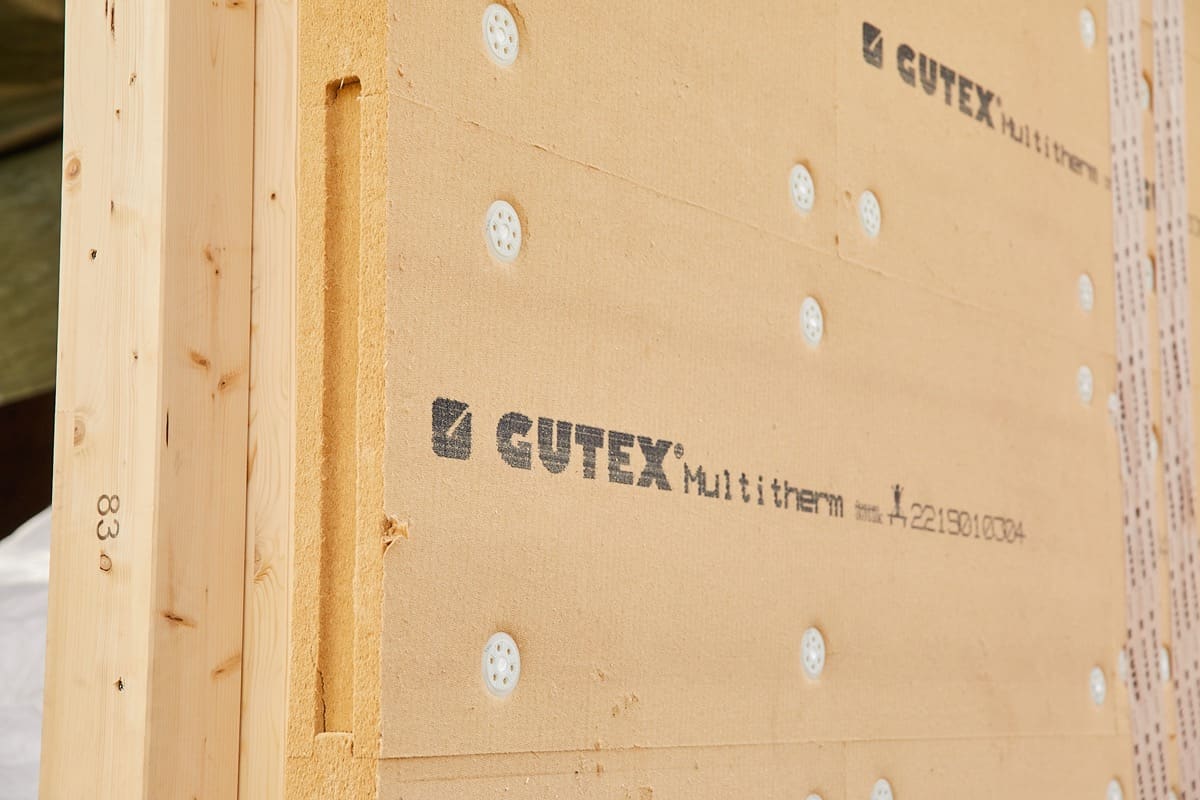
Wood fiber insulation boards consist of approx. 95% coniferous wood and a large proportion of waste wood. For the production, wood chips are shredded into wood fibers, which are then dried and mixed with polyurethane resin (PUR) and then pressed. The board is then cured in a drying oven and can finally be used. The material is excellent for thermal and sound insulation.
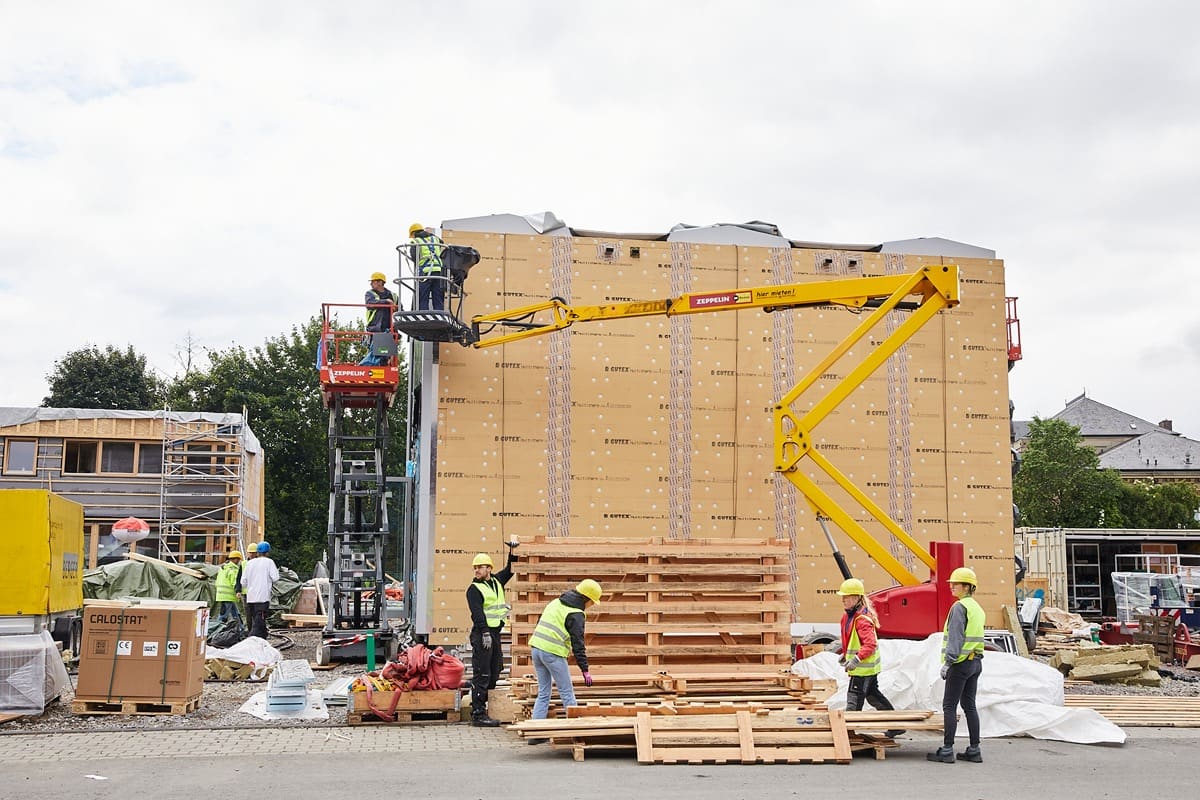
Wood fiber boards can be recycled simply and easily after use. This means that they can be separated by type from other building materials and simply reused for the same application. If the boards have to be disposed of, energy recovery in waste wood incineration plants is recommended. (Source: Gutex)
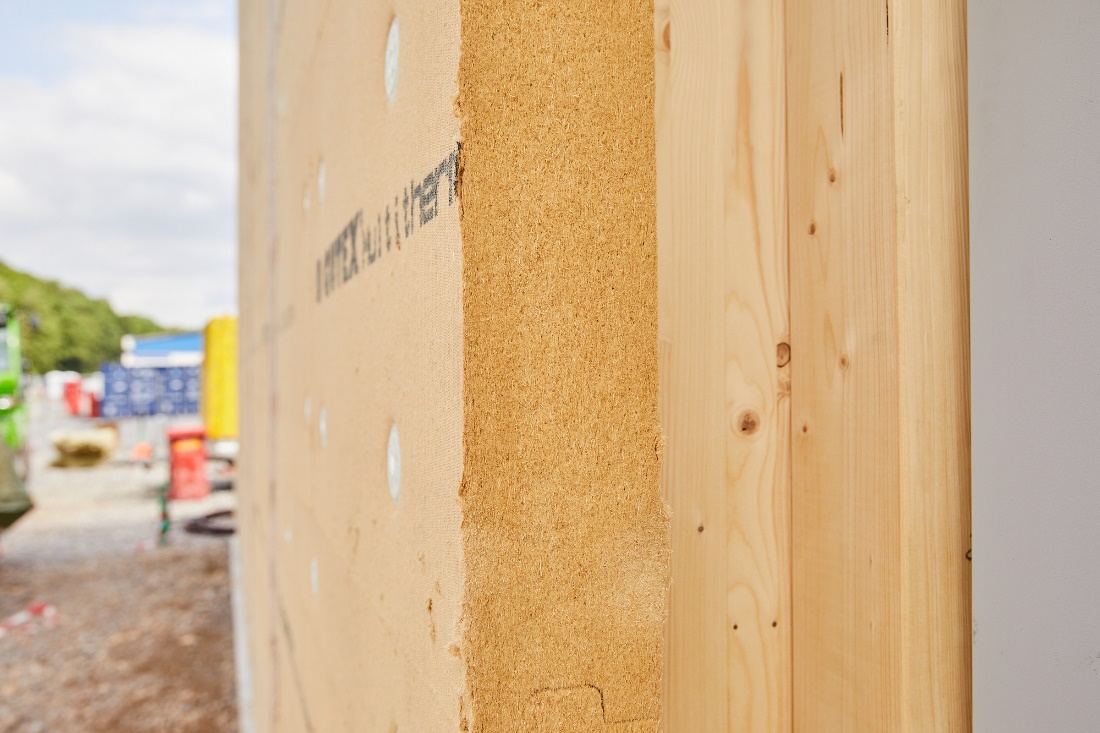
The panels are used in the HDU mainly hidden behind the north facade, as well as wall and floor insulation.
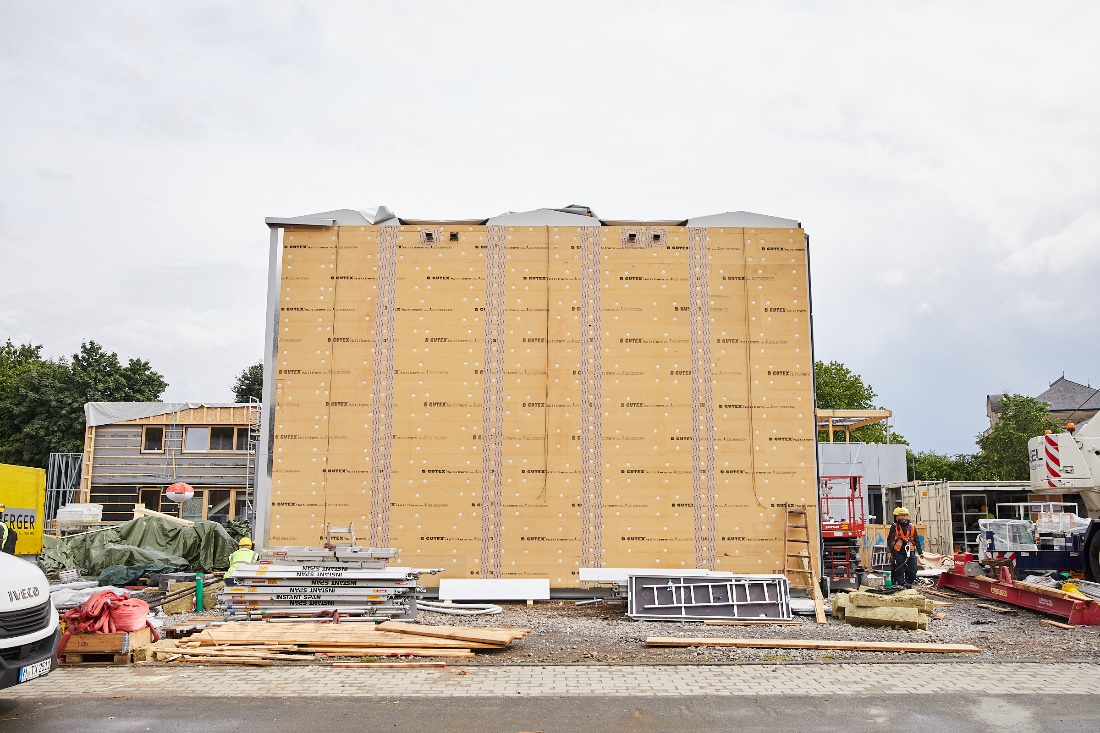
Massive Wood Parquet
Origin | Dresden, Germany |
Usage | Flooring |
Average bulk density | 665 kg/m³ |
Thermal conductivity | 0,17 W/(mK) |
Fire protection class | B2 |
Specific heat capacity | 1600 J/(kgK) |
CO₂ balance (global warming potential – GWP): | 85,07 kg CO2-Äquivalent/m³ |
Recycable, closed loop |
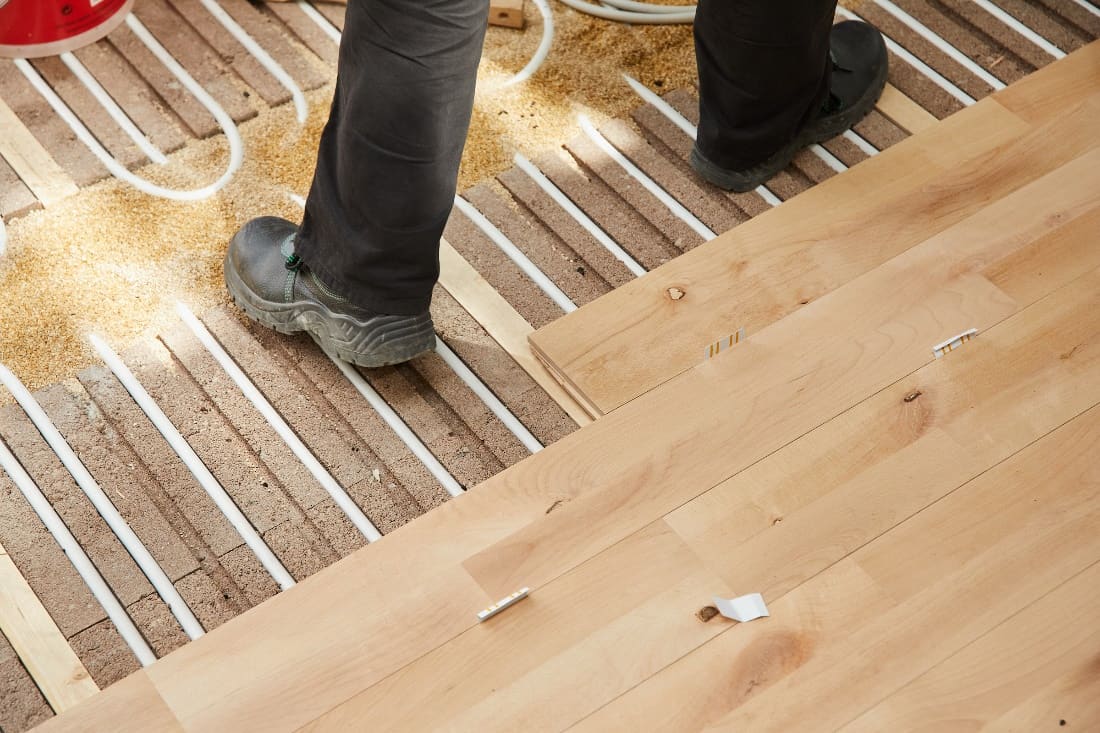
The solid wood parquet is beech wood. The clips of the individual planks are clicked into a pre-milled groove on the underside of the plank, holding the individual planks together. The clip-in system makes for easy installation, simplifies the replacement of individual planks, and is easy to take with you if you move. Solid wood planks have a long durability and can be sanded several times in case of soiling or even damage. The warm color as well as the material as such provides a feel-good atmosphere and a pleasant room climate. (Source: Junkers)
The parquet flooring is used in the modules as well as in the climate envelope.
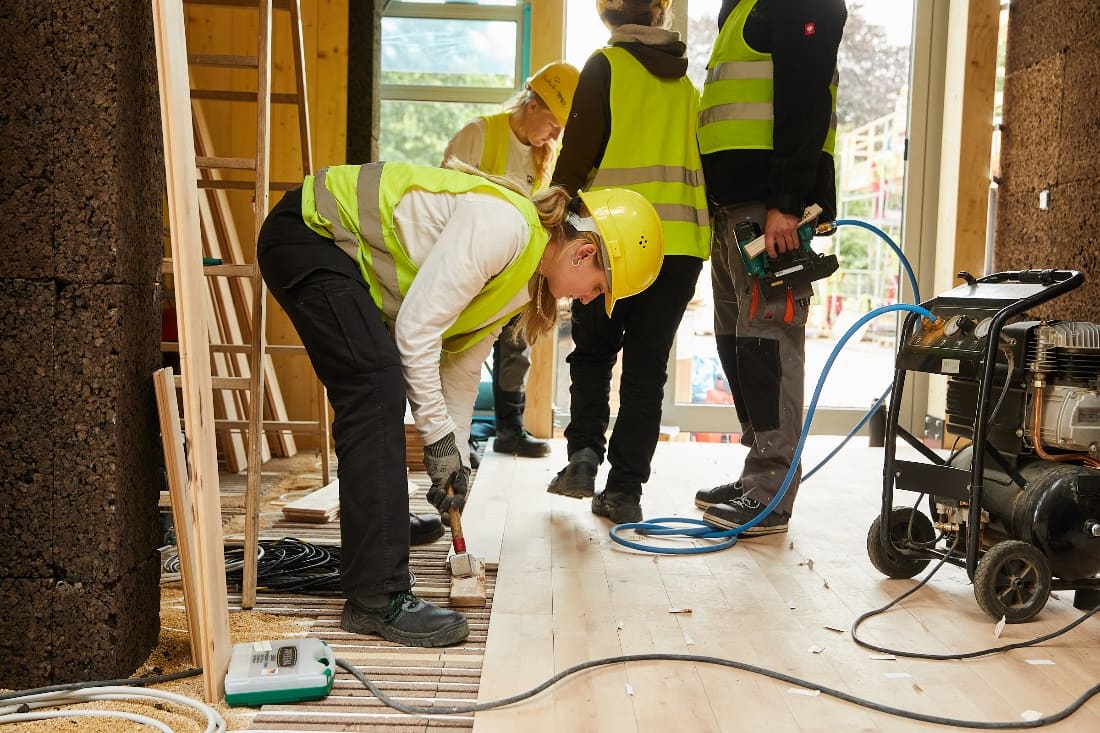
Clay
Origin | Viersen, Germany |
Usage | Plaster, clay block, clay building board (interior) |
Average bulk density | 120 kg/m³ |
CO₂-Bilanz (Treibhauspotential – GWP): | 0,12 kg CO2-Equivalent/m³ |
Recycable, closed loop |
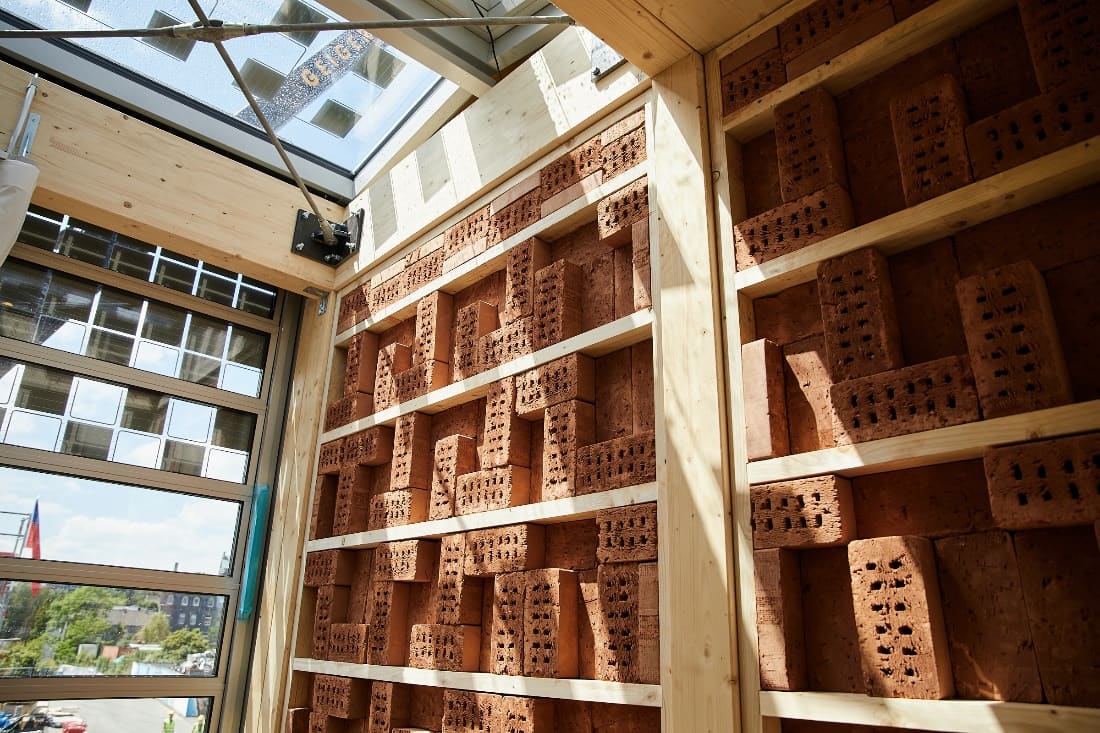
Clay is one of the oldest building materials in the world and of abiotic (inanimate) origin. In the pressing process, the clay can be pressed or pressed into wooden or clay forms (e.g. bricks). After complete drying, the materials can be used in a variety of ways. Clay has a very high durability and therefore cannot be composted, but can be reused infinitely. Thus, a closed material cycle is created with all clay products. Clay stores heat and thus regulates interiors, so that the heating effort and costs can be reduced. Clay creates a stable temperature and binds dust and odors and has been proven to reduce the risk of mold growth.
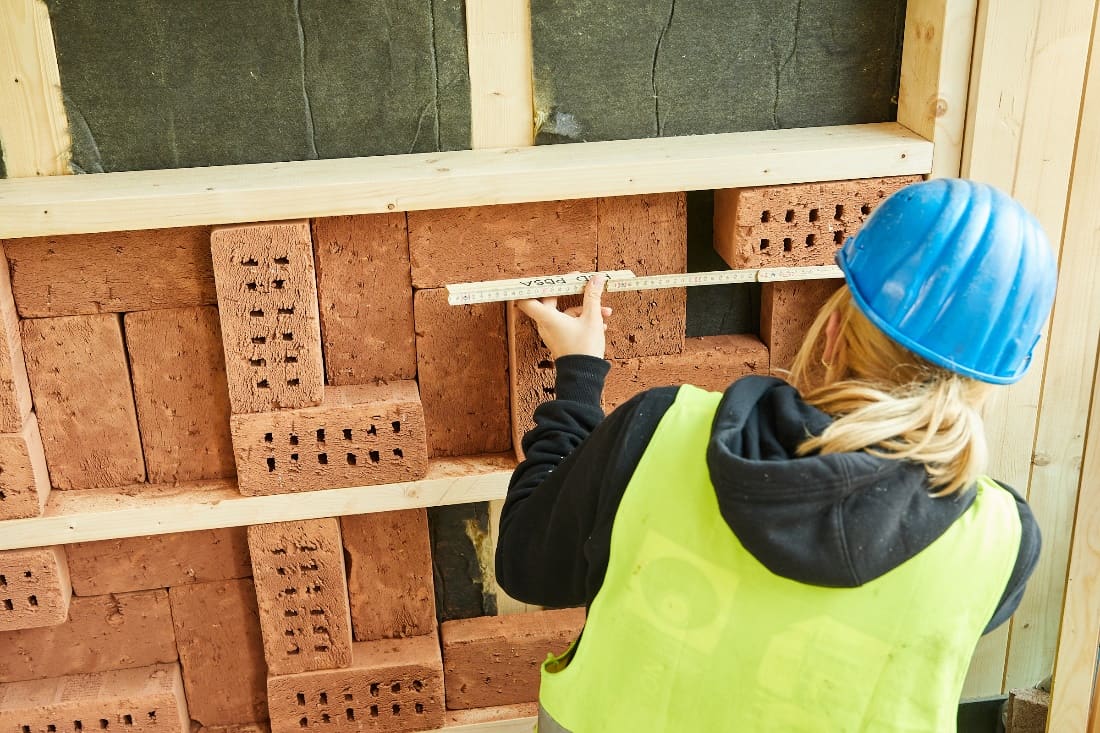
Clay is present in the interior of the north wall, but also the wall plaster in the living module is made of clay plaster.
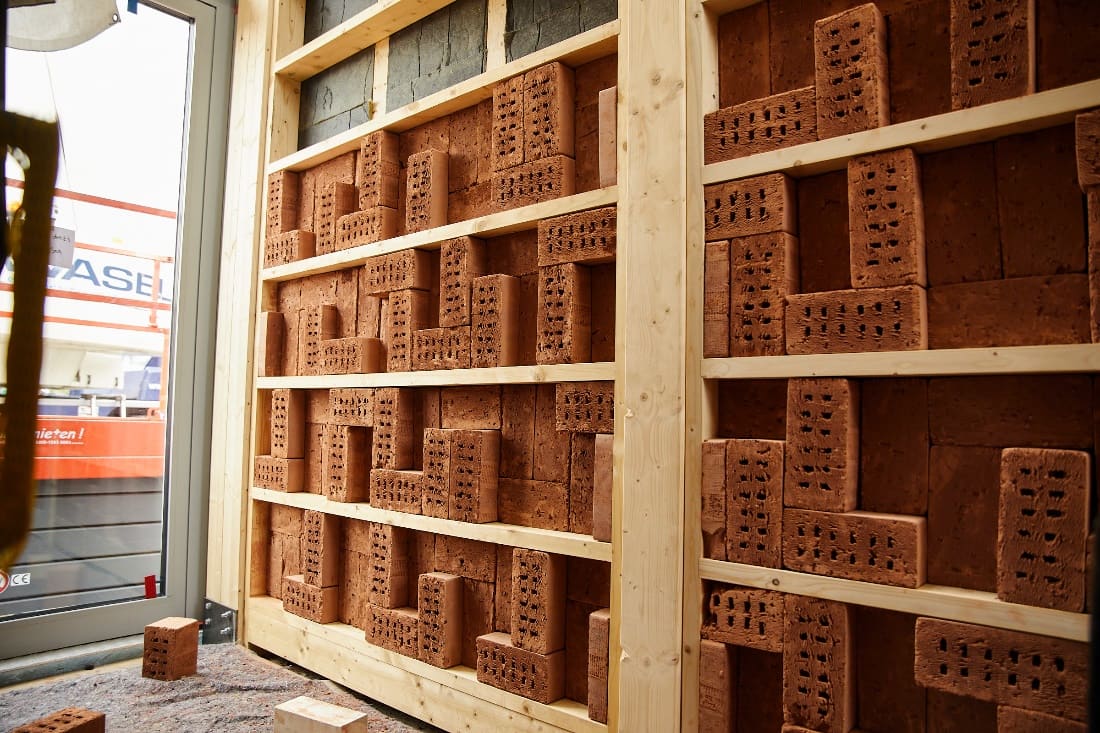
Underfloor heating
Origin | Uhler, Germany |
Usage | Underfloor heating |
Average bulk density | 1500 kg/m³ |
Thermal conductivity | 0,89 W/mK |
Fire protection class | A1 |
Specific heat capacity | 1000 J/kgK |
CO₂ balance (global warming potential – GWP): | 65 kg/m² |
Recycable |
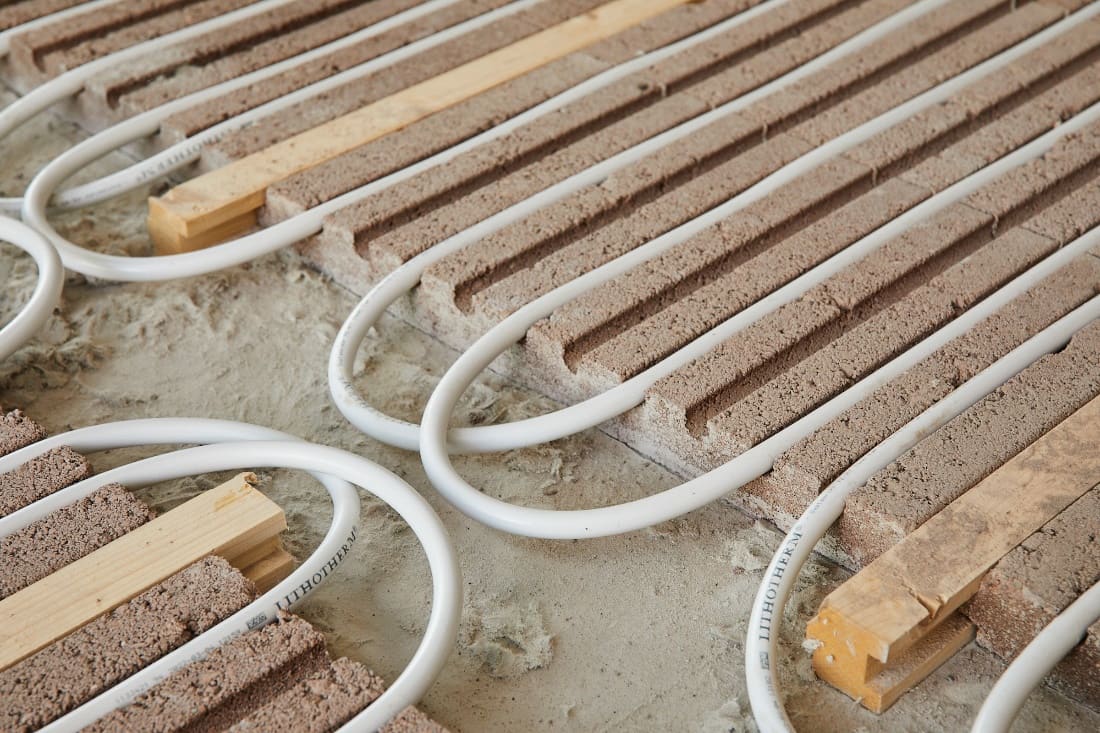
The flooring system consists of natural stone materials lava split, lime chippings and clay granules. The basalt lava stone serves as heat storage as well as sound and impact sound insulation. With a low flow temperature, the radiant heat can be delivered directly into the room. Minute regulation serves as the basis for perfect heat and humidity regulation in the interior. The materials provide good heat protection in summer and cold protection in winter. When used optimally, underfloor heating saves up to 4 KG of CO2 per m² per year. The natural building materials can be separated again after use and then recycled. (Source: Lithotherm)
The heater is located directly under the parquet in the climate envelope, thus heating the floor and regulating the temperature in the interior.
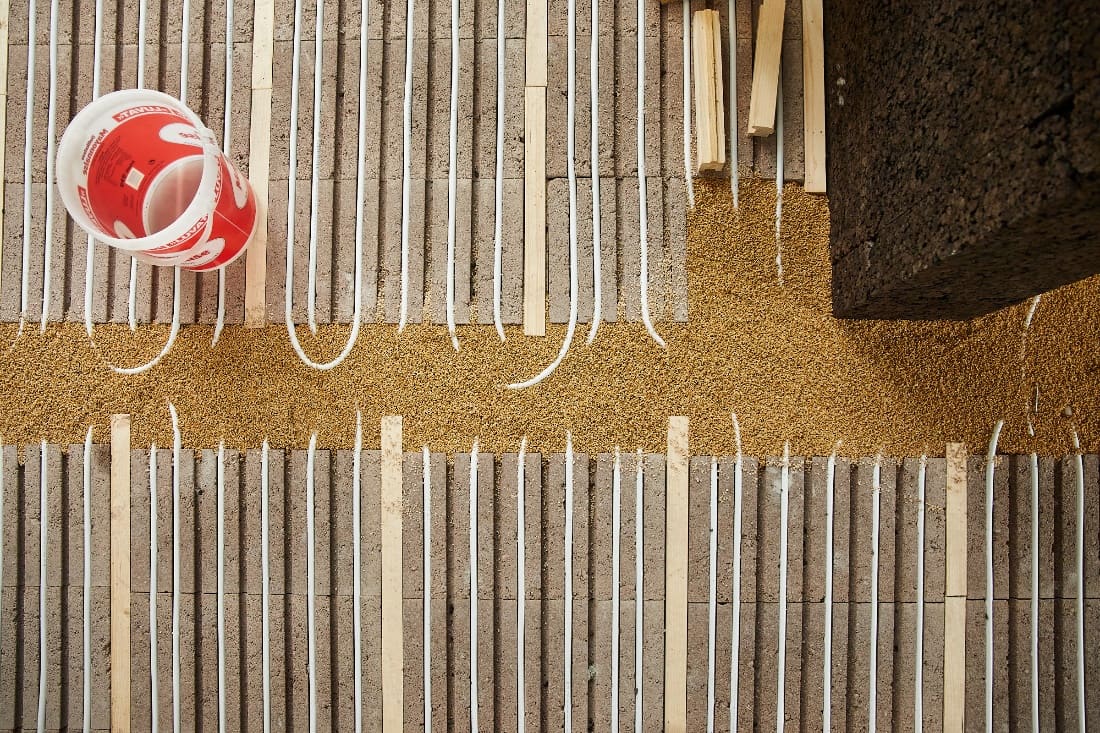
Mineral Wool
Origin | Gladbeck, Germany |
Usage | Perimeter insulation (earth boundary) |
Average bulk density | 39 kg/m³ |
Thermal conductivity | 0,032 – 0,05 W/(mK) |
Fire protection class | A1 |
CO₂ balance (global warming potential – GWP): | 132,44 kg CO2-Equivalent/m³ |
Recycable |
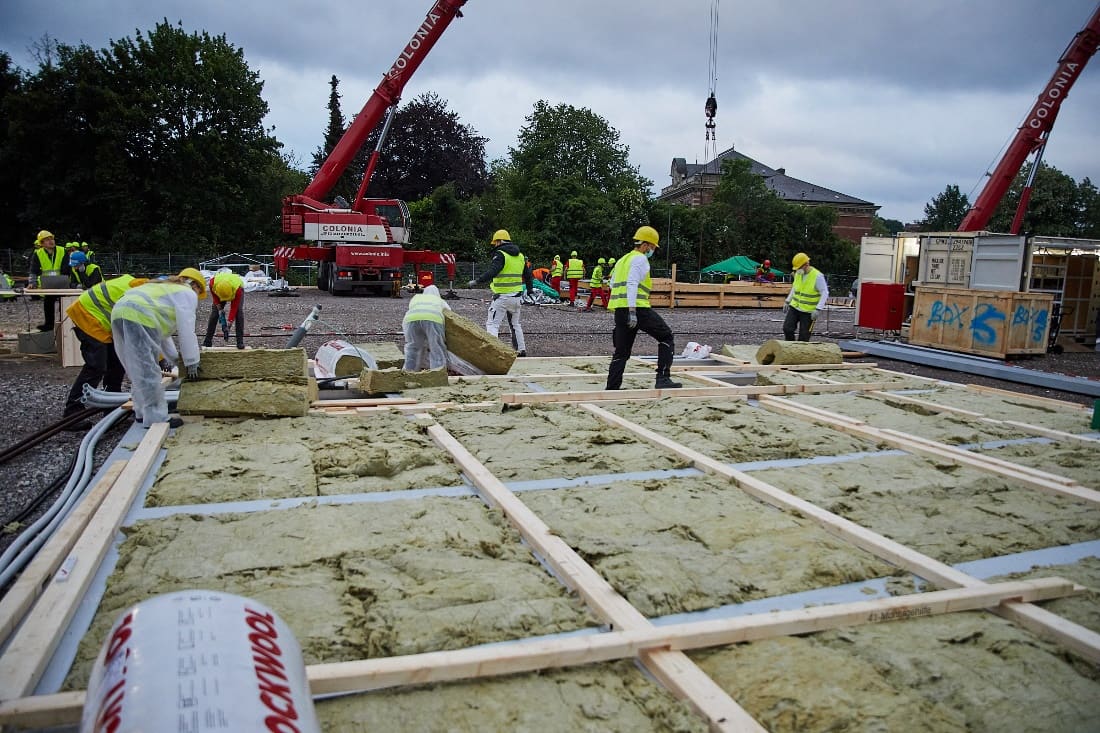
Mineral wool is of abiotic (lifeless) origin and is obtained from various rocks. These are heated and spun into fibers. Rock of volcanic origin is chosen as the basis, such as basalt in this case. Due to volcanic activity and earth plate movements, more basalt is produced than is used.
Around 96% of the rockwool residues can be reused in production. In addition, we have the advantage with the selected manufacturer (Rockwool) that it promises a manufacturer take-back when the building is dismantled. Whereby again the old mineral wool can be recycled. Moreover, only one cubic meter of raw material is used to produce about 100 cubic meters of rock wool.
The material has a long service life and has very good properties in areas such as sound, heat and moisture protection. Another advantage arises in fire protection, since rock can not burn. (Source: Rockwool)
The supporting grid, the north wall behind the clay blocks, as well as the parapet and corner points of the climate envelope are insulated with mineral wool.
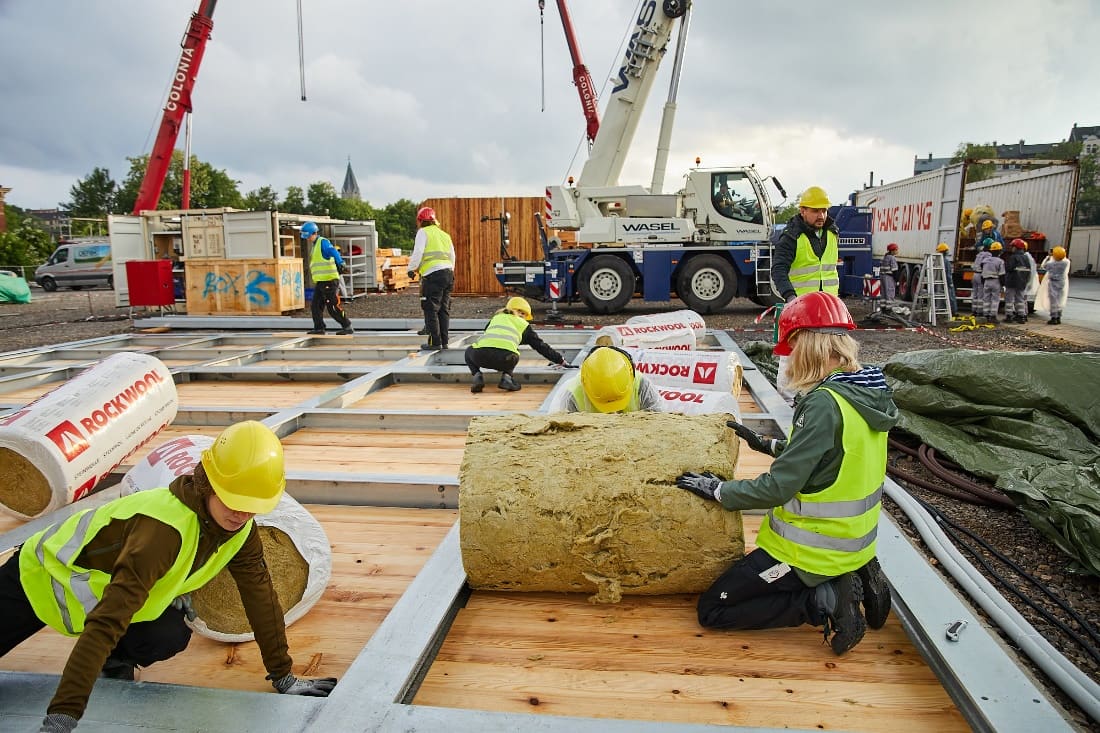
Wall heating
Origin | Göttingen, Germany |
Usage | Wall heating |
Weight | 36,5 kg/m² |
Thermal conductivity | 1,05 W/(mK) |
Fire protection class | A1 |
Recycable |
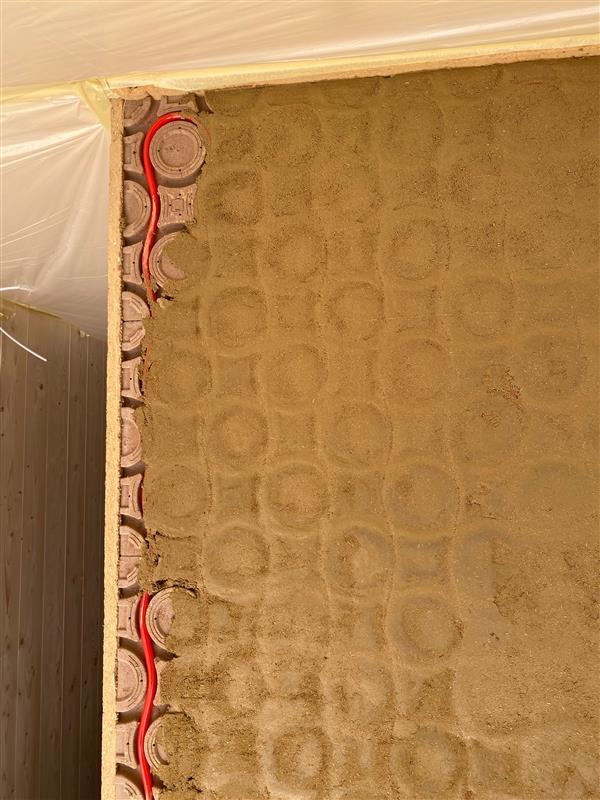
The circular wall heating system combines the positive properties of clay as a building material with innovative heating technology. For this purpose, a unique panel system was developed, which favors easy laying of heating pipes. The modular system enables wall heating that fits precisely and covers the entire area. The individual clay modules are attached to a substructure with screws and finally covered with a clay plaster. A short reaction time optimally tempers the room, the clay regulates humidity and additionally purifies the air. The comfort inside is increased by pleasant acoustics and a natural, lively material. (Source: Argilla Therm)
The wall heating is hidden behind the clay plaster in the living modules and is responsible for the temperature control here.
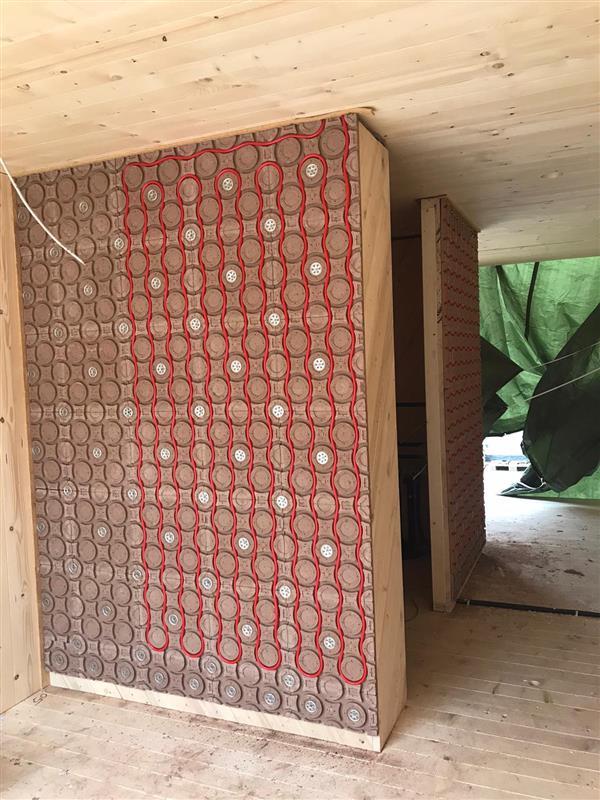
Myzel-Insulation
Origin | Germany |
Usage | Wall / Floor, Ceiling |
Average bulk density | 172 kg/m³ |
Thermal conductivity | 0,053 W/(mK) |
CO₂ balance (global warming potential – GWP): | 85,07 kg CO2-Equivalent/m³ |
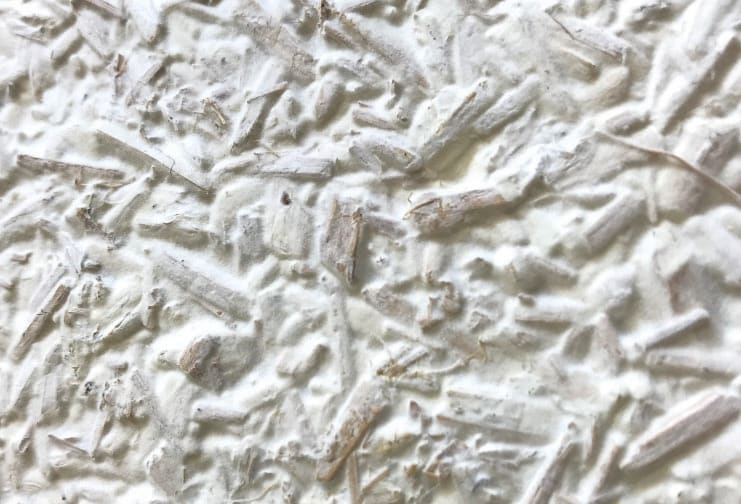
The mycelium is the root system of fungi. In combination with a biological substrate, it grows within 5-7 days in a negative form in a dark environment at about 22°C. Other components (such as plant stems, absorbent cotton, or expanded concrete) can be added to the mycelium to provide greater strength. As the root system grows, it binds the substrate and forms many small air spaces, providing a good insulating effect. After the growth phase, the mycelium can be dried by various methods (e.g. heat drying, freeze drying, vacuuming) before being used as insulation.
The product can be made in any shape and is 100% recyclable. After use, it can be shredded and used as a substrate for new mycelium. Since it is made of 100% biological materials, it can also be composted. The material is non-combustible, moisture regulating and free from any additives.
In our HDU, the Myzelium is used as insulation of a sandwich panel in the west facade. Through the use of a glass pane, the insulation is visible from the outside.
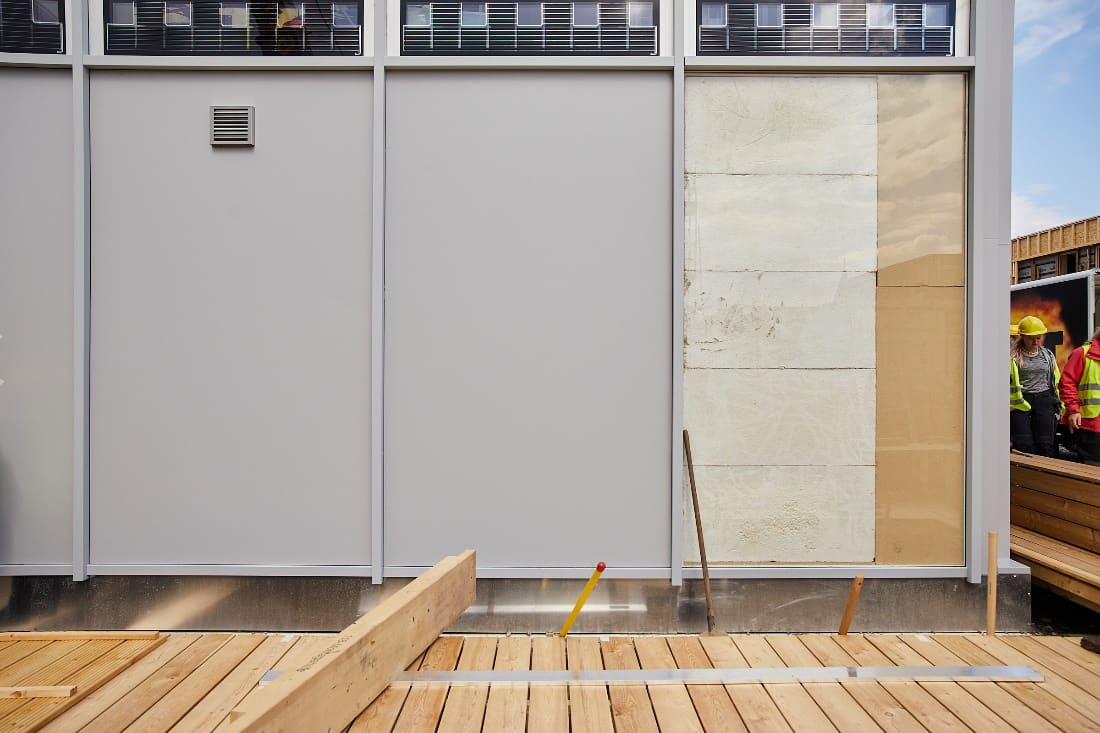